Tubular Heaters
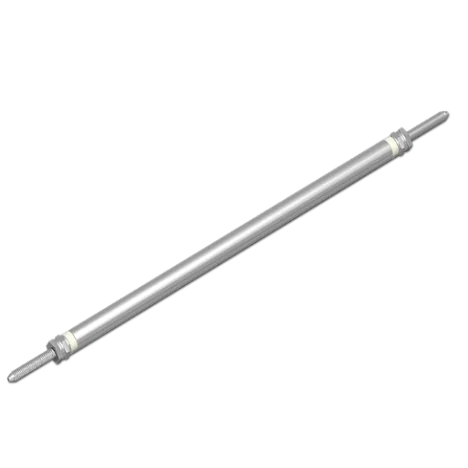
The configuration of tubular heaters can be straight or include one or more curves. Both immersion and air heating applications make use of them. They are employed in immersion applications more frequently. Furthermore, tubular heating applications are arguably the most dependable and adaptable in terms of power, terminations, materials, mounting options, and lengths. The Tubular heater can be customised to practically any customer request because of the wide range of application options available.
Tubular Heater Capabilities and Benefits:
- Small volume and large heating power.
- Constructed with epoxy or silicone seals to resist moisture contamination (Oxidation and corrosion resistance)
- Long service life, multiple protection system, safe and reliable
- It is possible to heat a variety of media under various conditions, including those that are explosion-proof; Three, the maximum heating temperature is 720 °C;
- Compacted with insulating MgO that allows heat to transfer away from resistance wire to the sheath material and media with faster efficient heat up.
- Virtually a limitless array of custom bend formation options, to include adapting heater element around space parameters – to maintain maximized efficient heating.
Tubular Heater Applications:
Platen heating, Metal mold, Tank heating, Freeze protection, Thermoforming, Medical and analytical device heating, Combi ovens, Rotisserie ovens, Steamers, Warming cabinets, Convection ovens, Conveyor ovens, Smokers, Fryers, Ware washers, Griddles, Radiant heating, Vacuum applications, Fluidized beds, and Circulation heating.We offer 0.430 and 0.315 inch diameter tubular heaters. Our tubular versions are now offered in lengths of up to 6′. Our tubular heaters are built through compression throughout the manufacturing process, including the creation of the bend(s) and the inner coil surrounded by compacted insulation from the sheath.
Tubular Heater Features:
- There are practically no limits to the custom bend creation choices that can be used, including tailoring the heater element to the specifics of the room in order to maximise heating effectiveness.
- Compacted with insulating MgO, which enables faster and more effective heat conduction from the resistance wire to the sheath material and media.
- constructed to withstand moisture infiltration with epoxy or silicone sealing (Oxidation and corrosion resistance)
- Incoloy® Sheath material (call to discuss other metal options as needed)
- Threaded fittings are brazed, crimped or welded to the cold section of the heater
- MgO insulation fills the sheath to maximize the dielectric strength, promote efficient heat transfer, and prolong the life of the heater.
- Stainless steel studs are welded to the terminal pins, which can be covered with protective Ceramic Terminal Covers
- Epoxy or silicone resin seals provide protection from moisture contamination. Seals can rate up to 390°F
- Nickel chromium Resistance wire is welded to the terminal pins for a stronger positive electric connection to increase the life span of the heater.